二氧化锆空心微球制备技术
与其他空心微球制备方法相似,空心二氧化锆陶瓷微球的制备方法众多,主要包括模板法、溶剂热法、喷雾干燥法和等离子烧结法等。模板法是以预先制备的模板作为内核进行空心颗粒的合成,模板的形状决定了空心颗粒的形貌;溶剂热、喷雾干燥和等离子烧结等方法制备空心微球的过程摒弃了使用模板作为基底,它们主要是利用Ostwald熟化过程进行空心结构的调控。以上这些制备手段同样广泛应用于氮化物[16]、碳化物[17]及其他氧化物[18]空心微球的制备上。
2.1 模板法
模板法是制备空心微球的一类常用方法[19,20]。模板法是在颗粒的制备过程中,采用液滴、气腔和胶粒等模板作为颗粒形成的基底,通过吸附、沉淀、界面反应等过程,在基底表面形成所需要的颗粒,再通过烧结氧化、化学腐蚀、氧化还原等过程去除模板,从而得到空心陶瓷微球[21]。模板法制备空心微球示意图如图1[21]所示。模板法具有原理简单、重复率高以及性能稳定等特点,近年来,越来越多的研究人员采用模板法进行二氧化锆空心微球的制备[11]。
图1 模板法制备空心微球示意图[21]Fig.1 Schematic diagram of hollow spheres prepared by templating process[21]模板法由于效率高、适应性强而得到了广泛的研究,制备ZrO2空心微球时常用的模板包括PS球、胶态碳球及生物模板等[22-24]。Liu等[25]以碳质多糖微球为硬模板,采用非均相成核包裹技术成功制备了粒径2 μm、壁厚约100 nm的ZrO2空心微球。首先将碳质多糖微球模板分散在乙醇中并与一定比例的氯氧化锆前驱物均匀混合,而后加热混合物使溶剂在稳定的温度下挥发,并向其中加入30% H2O2溶液;最后经冷却、离心、高温煅烧后得到ZrO2空心微球。研究发现,H2O2能够促进锆离子的水解和沉淀,并且碳质多糖微球可以较好地成为沉淀的形核中心并可通过后续的煅烧去除。高立爽等[26]以油菜花粉为生物模板,通过水浴-陈化法制备了纳/微米结构ZrO2空心微球。研究发现,花粉预处理方式对于ZrO2中空微球的形貌及壁厚具有重要影响。Guo等[23]以胶态碳球为模板制备了壳结构可控的ZrO2空心微球。首先以葡萄糖为原料,采用水热法制备胶态碳球模板;进而以氨水为pH调节剂、以氯化锆为前驱物得到Zr(OH)4/胶态碳球复合颗粒;最后经过离心、洗涤、煅烧后得到ZrO2空心微球。研究发现,制备过程中加入表面活性剂(聚乙二醇-1000)可以得到具有多孔壳结构的空心微球,从而实现空心微球壳结构的有效调控。Ge等[27]以CaCO3为模板,采用沉淀法成功制备得到了粒径1 μm、壁厚20 nm的ZrO2空心微球。首先进行CaCO3模板的制备并通过沉淀法得到CaCO3/ZrO2复合颗粒,再经过酸洗去除CaCO3模板,最后经过煅烧制备得到四方相ZrO2空心微球。研究发现,前驱物浓度和反应时间对空心微球的形貌和粒度有重要影响,前驱物浓度过大会导致实心颗粒的形成,反应时间过短容易形成不稳定的薄壁空心颗粒,因此,合适的前驱物浓度和反应时间对于采用模板法制备稳定的ZrO2空心微球至关重要。模板法在ZrO2空心微球形貌的控制上表现出色,但是存在模板合成及后续去除过程繁琐等问题,并且对于制备工艺的要求较高,容易造成材料的浪费以及空心微球的破坏。同时,空心微球的大小受制于模板的尺寸,目前模板法制备空心微球的尺寸多为10 μm以下,难以应用在喷涂领域。为了克服模板法制备空心微球所存在的缺点,实现较宽粒度范围的空心微球制备,研究人员提出了一些基于Ostwald熟化过程制备ZrO2空心微球的方法。
2.2 溶剂热法
溶剂热法是指在特制的密闭反应器中,采用有机溶剂作为反应介质,通过对反应体系加热加压而创造一个相对高温高压的反应环境,使得通常难溶或不溶的物质溶解并重结晶而进行目标材料制备的一种有效方法[28]。溶剂热法也是制备ZrO2空心微球的一种有效方法[29],它规避了模板的使用,因此不存在模板的合成及后续去除等问题。Guo等[30]以无水乙醇作为溶剂,以ZrOCl2⋅8H2O和Y(NO3)3⋅6H2O作为前驱物,并加入尿素和盐酸,在反应釜中于160℃反应12 h成功制备了粒径1.2~1.5 μm且壁厚约125 nm的YSZ空心微球。Shu等[31]在乙醇/丁醇-乙酰丙酮体系中,以ZrOCl2⋅8H2O和Y(NO3)3⋅6H2O为前驱物,采用无模板的溶剂热法制备了YSZ空心球。研究发现,空心球是基于颗粒由内而外的Ostwald熟化过程而形成的;并且可以通过调节醇的种类及前驱体的浓度实现YSZ空心球尺寸的有效调控。溶剂热法特有的高温高压环境使得反应物性能改变、活性提升,得到的空心微球具有粒径分布窄、形貌可控的优势。但是,溶剂热法的反应条件相对苛刻,并且涉及到产品的后续分离及洗涤、干燥等过程,难以进行批量化制备。
2.3 喷雾干燥法
喷雾干燥法是制备喷涂涂层用原料的重要方法,通过使用适当的有机黏合剂聚集不同的小颗粒进而从浆料中经干燥获取颗粒团聚体。浆料在干燥过程中发生快速传热和传质,根据操作参数、浆料特性的不同,得到诸如空心、致密、多孔等形态各异的球形或其他形状的颗粒团聚体[32,33]。喷雾造粒得到不同结构的团聚颗粒如图2[32]所示。浆料在喷雾干燥过程雾化为球形液滴后的快速干燥阶段,液滴中的水分快速蒸发产生毛细管力,进而液滴内部的细小颗粒在毛细管力的作用下向表面迁移并最终形成空心颗粒,如图3[34]所示。因此,在喷雾干燥过程中,浆料的分散性是决定团聚颗粒结构的关键因素,高分散性浆料中细小颗粒的迁移阻力更小,更有助于获取具有空心结构的颗粒团聚体。
图2 喷雾干燥制备颗粒的结构示意图[32]Fig.2 Structure diagrams of particles prepared by spray drying process[32]
图3 喷雾干燥制备空心颗粒的过程示意图[34]Fig.3 Schematic diagram of preparation of hollow particles by spray drying process[34]Mahdjoub等[35]和Bertrand等[36]研究了浆料特性对YSZ喷雾造粒颗粒结构的影响,通过调控浆料的pH值和引入表面活性剂来调控浆料的分散性,并通过沉淀高度比(Ratio Sediment Height, RSH, 即浆料静置90 h后,沉淀层高度与浆料总高度之比)来表示浆料的稳定性。当RSH<53%时,YSZ喷雾造粒颗粒基本为空心结构;当RSH>62%时则基本为实心结构;同时,空心颗粒的壁厚随着RSH减小而降低。Loghman-Estarki等[37]用喷雾干燥法进行适用于喷涂的YSZ纳米颗粒团聚体的制备,并研究了黏结剂PVA的含量对喷雾造粒颗粒特性的影响。研究发现,浆料中PVA的含量对喷雾造粒颗粒的形貌和粒度具有重要的影响。当浆料中不添加PVA时,得到的球形空心颗粒中存在较多的非球形多面体颗粒;当浆料中PVA含量为5wt%~15wt%时,喷雾得到的多为球形或准球形的颗粒。造粒颗粒的直径随着PVA含量的变化可以由经验公式(1)表示。

式中,SMD为索特尔中位粒径,C为常数且和雾化器设计有关,ρ, μ, σ, U和
分别表示液体(L)或空气(A)的密度、黏度、表面张力、速度和流量速率。当浆料中的PVA含量增大时,浆料的黏度随之增大,从而获得更大尺寸的喷雾颗粒。进一步地,Loghman-Estarki等[38]研究了球磨过程对于喷雾干燥颗粒特性的影响。首先采用湿化学法制备得到了尺寸30~50 nm的Y2O3和Sc2O3共掺杂的ZrO2纳米颗粒(SYSZ)[39],进而通过球磨法获取喷雾所需的浆料,最后经过喷雾干燥过程得到团聚颗粒。研究发现,球磨使得团聚的纳米颗粒得到较好的分散,并且有助于获取具有准球形形貌的空心颗粒。作者进一步研究了喷雾干燥制备团聚体的形成过程,喷雾干燥过程中热量经热传导的方式由颗粒表面传递到内部,关系式如式(2)所示。
, 0≤r≤R(t), t>0
式中,T为温度,k为热导率,ρ为密度,Cp为热容,r和R(t)分别表示颗粒径向直径及其径向位置,假设k不受径向位置和时间的影响,则式(2)可以转化为:
, 0≤r≤R(t), t>0
式中,
为热扩散系数,
=k/ρCp,热传递过程可以表示为:

式中,为热流量,A为接触面积,ΔT为温度差异。因此,喷雾浆料中的黏结剂PVA (p)和去离子水(w)的分解及挥发过程可以表示为:
|
|
|
(4)
|
|
, 0≤r≤R(t), t>0
|
(5)
|
其中,D为二元扩散系数,
是指黏结剂PVA (p)或去离子水(w)的含量。去离子水的蒸发温度为200~295℃,而PVA的分解挥发温度为300~571℃[38]。由于喷雾干燥的入口温度为225~235℃,因此去离子水可以较好的去除,而PVA则遗留在颗粒内。喷雾干燥法制备得到的YSZ空心粉体由于颗粒强度较弱,在喷涂应用的过程中容易破碎从而失去空心颗粒的特性,因此在使用前需要对颗粒进行高温烧结以提升其强度。
2.4 等离子体烧结法
等离子体烧结法是采用等离子体作为热源,通过对其他方式制备的多孔ZrO2团聚粉末进行热处理来制备空心球形颗粒的工艺方法[40]。等离子体具有温度高、传热快、冷却速率大等特点,是一种颗粒球化、烧结及新型材料制备的有效方法,国内外开展了大量的研究工作[41,42]。经过等离子体处理的粉末不仅具有良好的球形度和优异的流动性,而且在提升颗粒的致密性、机械强度等方面也具有显著优势。同时,等离子体技术在空心微球的制备上也具有良好的应用效果[43-48]。Zhao等[49]以喷雾干燥工艺得到的YSZ团聚粉末为原料,采用等离子体烧结法制备得到了壁厚3 μm的YSZ空心微球。作者通过控制颗粒离开等离子体火焰时周围环境的温度,实现了空心微球壁厚的有效调控。研究发现,在颗粒离开等离子体火焰后的区域内增加保温功能,可以防止颗粒表面的快速固化,使得YSZ熔融液滴充分膨胀,从而减小了空心微球的壁厚。Solonenko等[50,51]以喷雾造粒的ZrO2团聚颗粒为原料,采用等离子烧结技术进行ZrO2空心微球的制备。作者认为,喷雾造粒的ZrO2团聚颗粒通常是具有一定开孔孔隙率的非均匀结构;团聚颗粒在经过等离子体的高温火焰时,孔隙内的气体膨胀后部分离开颗粒,同时其表面迅速熔融而形成的液膜使得孔隙内的一部分气体得以封闭在颗粒内部;随着颗粒的进一步熔融,颗粒内部的气体形成空心结构,熔融的颗粒表面所形成的液膜在淬冷的环境下形成球壳,从而制备得到具有空心结构的ZrO2微球,其空心化过程如图4[50]所示。作者进一步对等离子体制备空心微球过程中团聚颗粒的变化进行了分析[50],等离子体中完全熔融的颗粒因为体积膨胀,颗粒尺寸增大,熔融颗粒半径的变化可以由式(6)得到。
图4 等离子体烧结形成空心结构的原理示意图[50]Fig.4 Principle schematic diagram of formation of hollow particles by plasma sintering process[50]
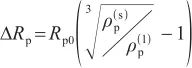
|
|
(6)
|
其中,Rp0为颗粒的初始半径,
和
分别表示固态和熔融态下颗粒的密度。熔融的颗粒经淬冷后,颗粒的半径Rps=Rp0+ΔRp;形成空心颗粒后,颗粒内部的空腔半径Rh=Rp0+ΔRp-h;因此,空心微球的壁厚h可以由式(7)计算得到。
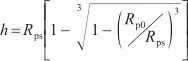
|
|
(7)
|
Qiu等[52]以中位径46.43 μm且空心比例不足10%的YSZ粉末为原料,采用三阴极等离子体炬烧结制备得到了球化率接近100%、颗粒中位径52.38 μm、空心颗粒比例93.4%且平均壁厚仅为3.63 μm的四方相YSZ粉末,合成的空心微球及颗粒的空心化过程如图5所示。
图5 等离子烧结法制备的空心微球及空心化过程[52]:(a), (b) 空心微球截面显微图像; (c) 空心化过程示意图Fig.5 YSZ hollow microspheres prepared by plasma sintering and their formation process[52]: (a), (b) microscopic images of the cross-section of hollow microspheres; (c) schematic diagram of formation process of YSZ hollow microspheres研究者将等离子体烧结制备空心微球的过程分为熔化、体积变化及固化三个阶段。在熔化阶段,粉末中的气体被加热、膨胀、逃逸,若等离子体提供的焓不足,则难以将粉末熔化,热壁喷嘴可以提供足够的焓以及适合的粉末加热速率使得颗粒中的大部分气体得以保留,从而确保了颗粒的球化率及颗粒中的气体含量;在体积变化阶段,液滴内部气体压力、表面张力及环境压力三者间保持平衡[51],提升初始团聚粉末的孔隙率、提高等离子体射流的温度以及降低等离子体射流的内部压力将更有助于获得薄壁空心颗粒;在固化阶段,适当降低液滴的冷却固化速率将更有助于获得高空心化率的粉末。因此,等离子体烧结法制备ZrO2空心微球时,所用前驱物的特性、等离子体参数的优化以及烧结过程的控制都将对空心微球的性能产生重要影响。ZrO2空心微球不同制备方法的特点如表1所示。模板法是制备空心微球的常用方法,模板法制备的ZrO2空心微球具有粒度分布窄、空心化率高等优势,但往往存在模板合成及后续去除过程繁琐等问题。溶剂热法制备空心微球时不使用模板,得到的粉体具有粒度分布窄、形貌可控的优点,但是溶剂热法反应条件苛刻,难以进行批量化制备。喷雾干燥法和等离子烧结法是批量制备喷涂用ZrO2空心微球的重要方法,其中喷雾干燥法得到的空心颗粒强度较低。等离子体烧结后制备得到的空心微球强度相对较高、流动性好,可以直接用于等离子喷涂。
表1 ZrO2空心微球制备方法总结Table 1 The summary of preparation techniques of ZrO2 hollow microspheres
喷雾干燥和等离子体烧结法联用更有助于制备适用于喷涂的高强度ZrO2空心微球,并且颗粒具有球形度好、流动性优异且易于批量化制备的优势。本课题组将喷雾干燥工艺与热等离子体动态烧结过程相耦合,进行了一系列诸如Al2O3, SiO2, Si3N4及ZrO2/YSZ等空心微球的制备研究工作,并详细考察了浆料特性对喷雾干燥颗粒形貌结构的影响以及热等离子体动态烧结对颗粒结构的调控过程[40,45,53,54],最终得到的YSZ空心微球如图6所示。
图6 不同方法制备的YSZ空心颗粒:(a) 喷雾干燥法; (b) 喷雾干燥和等离子体烧结联用Fig.6 YSZ hollow particles prepared by different methods: (a) spray drying process; (b) spray drying combined with thermal plasma sintering
3 结语与展望
随着科学技术的进一步发展,ZrO2空心微球的制备方法必将进一步地丰富和完善。当下,在众多ZrO2空心微球的制备方法中,模板法和溶剂热法等制备手段存在工艺过程复杂、合成条件苛刻且批量化制备困难等不足,并且有限的粒度调控范围使其难以在喷涂领域获得较好的应用。喷雾干燥法和热等离子体动态烧结法联用是制备应用于喷涂领域高强度ZrO2空心微球的有效方法,该方法不仅工艺简单、反应参数调控范围较大,而且制备得到的空心颗粒球形度高、流动性好,适合大规模生产;但是该方法制备空心微球的粒径和壁厚的调控难度相对较大,且颗粒空心化的具体过程还有待进一步证实。以上问题的顺利解决,必将推动ZrO2空心颗粒在隔热涂层和轻质隔热陶瓷等领域的应用。
氧化锆球是一种高纯度、高熔点(2700℃)、高硬度(接近钢铁)的陶瓷材料。因其优秀的物理、化学特性被广泛用于精密磨料、金属炼化、催化剂、钢铁生产、热处理、烧结等领域。而且,其不仅具有良好的磨损性能、抗腐蚀性能和温度稳定性,而且比钢铁具有更好的化学稳定性,因此可以用来制造精密陶瓷零件,比如机械密封零件、绝缘零件等。本文将从以下三个方面探讨氧化锆球的知识点:
1. 制作方法
2. 物理、化学特性
3. 应用领域
1. 制作方法
制作方法主要分为两种:喷雾干燥法和顶空烧结法。
喷雾干燥法
喷雾干燥法是将氧化锆精粉和水混合,在高速喷雾器中将水雾化,形成氧化锆颗粒,然后将颗粒输送到干燥器中,去除水分,形成颗粒状的氧化锆。最后再将氧化锆颗粒进行球形造粒和烧结。这种方法生产的氧化锆球,其表面光滑度好,球形度高,并且粒径分布均匀,但体积密度较低。
顶空烧结法
顶空烧结法是将氧化锆粉末制成模型,并在模型内部喷涂一层高分子丙烯酸(PAA)膜,然后将模型放入高温炉中进行烧结,使PAA膜分解形成空腔,在高温下,氧化锆粉末颗粒相互结合,形成球形氧化锆。这种方法生产的氧化锆球,其密度高,硬度大,重量均匀分布,但表面有些粗糙。
2. 物理、化学特性
氧化锆球是一种结构致密的陶瓷球,它具有以下几个重要的物理、化学特性:
硬度和磨损性能: 硬度接近于钢铁,远高于传统的玻璃、陶瓷等材料。因此,其具有良好的磨损性能,抗磨损生物陶瓷材料、医疗设备、高温磨料材料等领域得到广泛应用。
抗压强度和耐压缩性:其耐压强度接近于钢铁,并且具有良好的耐冲击性。因此,其可以用于高压磨矿领域、高速运动传动件、气体静压轴承和机械密封零件等高负荷工作环境。
抗腐蚀性能:主要组成成分为氧化锆,不含铁元素。因此,不易生锈,耐腐蚀性能好,可以用于催化剂、化学反应器等生产领域,也可以用于在海洋、化工等腐蚀环境下的应用。
温度稳定性: 具有高温稳定性,因为它的熔点高达2700℃,使其能够承受高温热处理。同时,氧化锆球在高温下也能保持其抗磨损性、硬度和耐压强度等优异的物理化学性能。
3. 应用领域
由于其具有优异的物理化学性能,因此在许多工业领域中得到广泛应用,主要包括以下几个方面:
精密磨料: 硬度高、磨损性能好,可以制成磨粉或磨球,作为高精度表面处理、抛光、切割等高精度加工领域的磨料。氧化锆磨料粒度均匀,表面光滑度好,能够保证加工零件的表面质量。
金属炼化:高温稳定性好,可以用于高温环境的精炼炉,作为流体的搅拌材料。此外,在钢铁生产中,也可以被用作喷吹嘴,起到控制流体流动的作用。
催化剂: 在化学反应中具有良好的交互催化作用。因此,它可以用作不同环境下的催化剂媒介。例如,二氧化氮还原反应、氧化亚氮还原反应、甲烷催化剂等。
钢铁生产:作为钢中间合金的添加剂,可以提高钢的硬度、韧性等物理机械性能。该材料还可以用作钢坯直径的调整媒介,使其达到技术要求。
绝缘材料:绝缘性能也非常强,可用于制造高压绝缘零件等。
总之,由于氧化锆球的优异物理、化学性能,它在各个领域中均得到了广泛应用,为各个行业带来了很大的改善。
二、氧化锆球物化指标
三、氧化锆球常规尺寸